Fire and Forge: The BlacksmithBy Susan Bush 12:00AM / Saturday, June 25, 2005
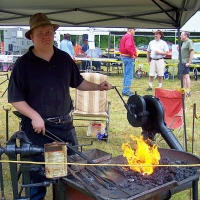 | Blacksmith Michael Tennyson fired up a portable forge. | Even during modern times, the skills and craftsmanship associated with the forge and fire blacksmith trade may be passed from one generation to another.
Master, Mentor, Muse
Michael Tennyson, 24, is considered a journeyman blacksmith, Tennyson said while working at a portable forge during a recent Town of Florida bicentennial celebration. Tennyson began learning the craft at age 12, and honed his skills under the guidance of his uncle, master blacksmith William Senseny of Williamstown.
Senseny acknowledged his nephew’s accomplishments during a June 23 interview.
 The beginning stage of a rose petal section. | “Michael has his own shop and business and he’s traveling about getting exposure and experience,†Senseny said.
Tennyson has clearly shown himself an apt student; he assisted Senseny with a major project that meant reconstructing an original set of iron gates at historic Fort Ticonderoga. The about 300 year old gates were damaged when a tractor-trailer truck crashed through them during a vehicle collision, and the precise repairs required a year’s work, both Tennyson and Senseny said.
“It was quite a project,†said Tennyson.
“The idea is to save as much [of the original craftsmanship] as possible and not create more damage,†Senseny said. “There were repairs needed and it was a year-long restoration.â€
Senseny teaches blacksmith arts through a series of courses that offer levels of apprenticeship, journeyman, craftsman, and master trainings. The workshops focus on skills including forging, cutting, splitting, fire building and maintenance, forge welding, and introductions to various tools. Workshops become more complex as skill levels increase.
The process is a bit different from the apprenticeships of yesteryear, Senseny and Tennyson noted.
Seven-Year Hitch
“In the bygone days, apprentices were usually permitted to use only small or large sledgehammers [for shaping] until they reached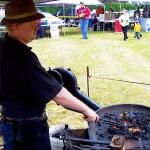 Tennyson heated the steel to about 3,000 degrees F. | certain skill levels,†Tennyson said.
“Experience is the delineator [among skill levels],†Senseny said. “Today, in the United States, there’s no real apprentice, journeyman or master certification.â€
“Historically, apprentices started at between 7 and 12 years old, and apprenticeships lasted about seven years,†Senseny said. “As the time went by, the apprentice took on more responsibility.â€
Apprentices often lived and worked with the master blacksmith, and began their careers by doing very menial tasks around the shop.
“He [an apprentice] would have gone on to become a good helper with the sledgehammer,†Senseny said. “At the end of the seven years, the contract would be over. The apprentice could choose to stay with the master or roam about the countryside learning more from other master blacksmiths.â€
A common goal was to set up one’s own blacksmith shop and craft tools, horseshoes, and other necessary items from forged metal.
Steel in Bloom
 Just one of many manual manipulations of the hot metal. | At the Florida bicentennial event, clad in an apron while deftly operating a bellows and handling tools that included hammers, chisels, an anvil and white-hot metal, Tennyson hand-crafted a section of a rose petals.
The bellows was turned by hand to force air onto hot coals and generate flames. Tennyson used 16-gauge steel for the rose section, and as he placed the dark, dull metal into the flames, he noted the heat level needed to soften the metal.
“This will be heated at about 3,000 degrees [Fahrenheit],†Tennyson said, as he used tongs to move and turn the metal.
The piece was removed from the heat for a first working, and Tennyson pounded the metal into shape with a French pattern cross peen hammer – an 80-year-old authentic smithing tool from France. The tongs Tennyson used were hand-made from hard-carbon steel, he said.
Tennyson worked the metal and returned it to the flames several times. Each time the piece was removed from the heat, Tennyson placed it on an anvil and used hammers and chisel-like tools to shape and detail the petals. The heat caused the piece to expand and grow a bit larger. Finally, the completed piece was dipped in cold water to cool it. The end result was a shiny, well-designed adornment. To make a full rose in bloom, Tennyson would have to make several more petal sections, a stem, several leaves, and then assemble the pieces, he said.
“My first rose took about 16 hours, now I can do it in about five hours,†he said, and noted that the one section he’d just completed required about 25 minutes of constant work. The finished product. More sections are needed to complete a metal full-blooming rose scuplture. |
Hot Opportunities
Modern-day blacksmiths are often working as artists more than as technicians, since many items once crafted by blacksmiths – nails, latches, hinges, tools and gates among them- are now mass-produced. Farriers, whose skills differ from those of a blacksmith, now do most horseshoeing.
The evolution has opened new doors for blacksmiths, according to information available at Senseny’s Internet Web site.
“[A blacksmith] can work larger for interior design and architectural applications, or smaller, making jewelry and damascus blades,†Senseny wrote. “New tools and techniques have opened up whole new areas for wrought iron design.†When asked if he will strive to reach the “master†level, Tennyson paused.
“Maybe,†he said. “Someday, maybe.â€
Tennyson may be reached at his shop by calling 802-722-3714.
Senseny may be reached by calling 413-458-4641. Additional information about Senseny is available at www.geocities.com/ironrestoration@sbcglobal.net.
Susan Bush may be reached by calling 802-823-9367 or by e-mail at suebush123@adelphia.net. |